Understanding the Impact of Technological Advancements in Blow Molding In the dynamic world of the blow molding industry, technological advancements have…
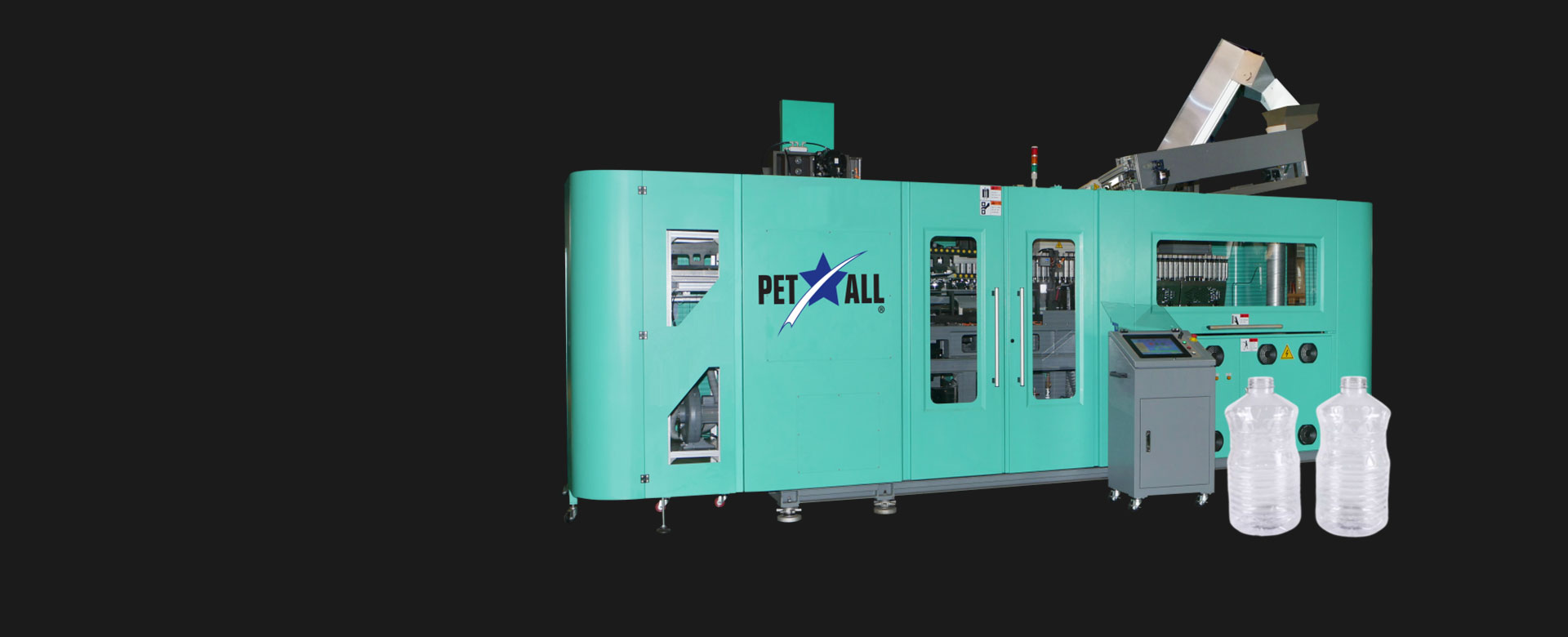
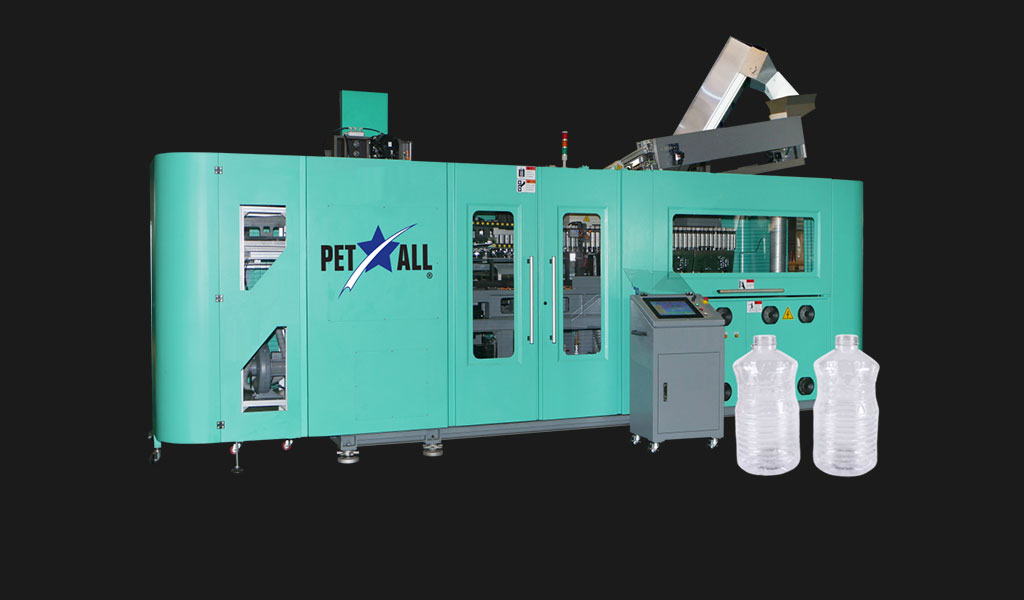
Categories: blow molding , Plastic Industry , Product Quality , Technology , production efficiency
Understanding the Impact of Technological Advancements in Blow Molding In the dynamic world of the blow molding industry, technological advancements have…
Click Here To Read The Full Article
Categories: blow molding , Customization , Efficiency , quality , Plastic Bottle Production
Embracing Customization in Blow Molding In the rapidly evolving landscape of plastic manufacturing, the demand for customization in blow molding…
Click Here To Read The Full Article
Categories: blow molding , energy efficiency , plastic production , sustainability
Understanding the Importance of Energy-Efficient Blow Molding In the rapidly evolving world of plastic production, energy-efficient blow molding has emerged as…
Click Here To Read The Full Article
Categories: Blow Molding. Machine , Plastic Bottle , Extrusion Blow Molding , plastic
In the extrusion blow molding (EBM) process a hollow tube of molten material, called a parison, is extruded out of…
Click Here To Read The Full Article
Categories: Advanced Technology , blow molding , ROI , production efficiency
Understanding the Importance of ROI in Blow Molding In the competitive world of plastic bottle production, maximizing return on investment (ROI)…
Click Here To Read The Full Article
Categories: blow molding , plastic production , Technology Innovation
Embracing the Future: Blow Molding Technology in Plastic Production In the dynamic world of plastic production, efficiency and innovation are not…
Click Here To Read The Full Article
Categories: blow molding , Bottles. PET Stretch Blow Molding , Machines , Plastics
While a previous article focused on uneven wall thickness distribution I’ll explain some of the other problems that processors are…
Click Here To Read The Full Article
Categories: blow molding , energy efficiency , Manufacturing , plastic production
Understanding the Dynamics of Blow Molding Efficiency In the competitive world of plastic production, the quest for efficiency has never been…
Click Here To Read The Full Article
Categories: blow molding , Customization , Manufacturing Efficiency , Plastic Bottle Production
Understanding the Need for Customizing Blow Molding Equipment In the ever-evolving landscape of plastic bottle production, the demand for customizing blow…
Click Here To Read The Full Article
Categories: blow molding , Efficiency , North America , plastic production , Technology
Understanding the Impact of Modern Blow Molding on Plastic Production Efficiency In the competitive landscape of plastic production, North American plastic…
Click Here To Read The Full Article
Categories: blow molding , plastic production , Technology Advancements
Understanding the Landscape of Blow Molding Technology As a key player in the plastic bottle production industry, you are undoubtedly aware…
Click Here To Read The Full Article
Categories: blow molding , Technology Advancements , Plastic Bottle Production , production efficiency
Understanding the Evolution of Blow Molding Technology In the dynamic world of plastic bottle production, staying ahead of the curve means…
Click Here To Read The Full Article
Categories: Accumulator Head Machine , blow mold , blow mold machine , bottle , Extrusion Blow Mold , Injection Blow Mold , machine , new technology , PET Reheat Stretch Blow Mold , plastic
All too often I go into a plant and work on a machine that is set to full clamp tonnage…
Click Here To Read The Full Article
Categories: blow molding , Manufacturing Technology , production efficiency , sustainability
Understanding the Role of Advanced Blow Molding Equipment in Modern Manufacturing In the ever-evolving world of plastic bottle production, staying ahead…
Click Here To Read The Full Article
Categories: blow molding , Customizable Equipment , plastic bottle manufacturing , production efficiency
Enhancing Production Efficiency with Tailored Machinery In the competitive landscape of plastic bottle manufacturing, efficiency and precision are paramount. Companies are…
Click Here To Read The Full Article
There are three types of reheat stretch blow molding machines used to convert preforms into bottles: Rotary machines Linear machines with continuous…
Click Here To Read The Full Article
Categories: blow molding , Manufacturing , Technology Innovation , production efficiency
Introduction In the fast-paced world of plastic manufacturing, staying ahead of the curve is not just an advantage—it's a necessity. As…
Click Here To Read The Full Article
Categories: blow molding , energy efficiency , plastic production , sustainability
Introduction In today's environmentally conscious world, sustainability in plastic production is more critical than ever. As industries strive to reduce their…
Click Here To Read The Full Article
Categories: blow molding equipment , machinery upgrades , Plastic Bottle Production
Understanding the Importance of Machinery Upgrades in Plastic Bottle Production In the fast-paced world of plastic bottle production, staying competitive requires…
Click Here To Read The Full Article
Categories: blow molding , modern machinery , plastic bottle manufacturing , production efficiency
Introduction In the competitive world of plastic bottle production, efficiency is paramount. As industries strive to meet increasing demands, the need…
Click Here To Read The Full Article